真空爐石墨模具是以高純度石墨材料制成的精密熱工部件,專為真空環(huán)境下的高溫加工設(shè)計。其核心特性源于石墨材料的天然優(yōu)勢:熔點(diǎn)達(dá)3850±50℃,在3000℃惰性氣氛中仍能保持結(jié)構(gòu)穩(wěn)定,配合低熱膨脹系數(shù)特性,可實(shí)現(xiàn)高溫急冷急熱工況下的零裂紋運(yùn)行。典型產(chǎn)品如T707系列密度達(dá)1.85g/cm³,肖氏硬度65,抗壓強(qiáng)度115MPa,抗折強(qiáng)度51MPa,兼具機(jī)械強(qiáng)度與韌性。廣泛應(yīng)用于航空航天、汽車制造、冶金、機(jī)械等領(lǐng)域。在這些領(lǐng)域中,石墨模具用于制造各種高溫合金、精密零件和特殊材料,為工業(yè)生產(chǎn)提供了重要的支持。
1、開裂問題
原因:
加熱或冷卻速度過快,導(dǎo)致熱應(yīng)力過大,使模具產(chǎn)生裂紋。例如在高溫下迅速冷卻,石墨模具內(nèi)外溫差大,收縮不一致。
石墨模具本身存在缺陷,如內(nèi)部有微裂紋、氣孔等,在使用時這些缺陷會擴(kuò)展,導(dǎo)致開裂。
受到外力沖擊,如在安裝、取出工件過程中操作不當(dāng),使模具受到碰撞。
解決方法:
優(yōu)化加熱和冷卻過程,采用緩慢的升溫和降溫速度,避免溫度急劇變化。例如在加熱時,先以較低的速率升溫,使模具均勻受熱,然后再逐步提高升溫速度;冷卻時,也采用類似的緩慢降溫方式4。
在制造模具時,嚴(yán)格控制原材料質(zhì)量和加工工藝,減少模具內(nèi)部的缺陷。對石墨材料進(jìn)行充分的烘干和預(yù)處理,去除水分和揮發(fā)物,降低其在高溫下產(chǎn)生氣體的可能性,從而減少因氣體釋放導(dǎo)致的開裂風(fēng)險4。
在操作過程中要小心謹(jǐn)慎,避免對模具造成碰撞和沖擊。使用合適的工裝夾具來固定和取放模具,確保操作的平穩(wěn)性。
2、氧化問題
原因:
真空爐內(nèi)雖然處于真空環(huán)境,但在高溫下,石墨仍可能與微量氧氣發(fā)生反應(yīng),導(dǎo)致氧化。特別是在真空度不夠或爐內(nèi)氣氛中含有雜質(zhì)氣體時,氧化現(xiàn)象更容易發(fā)生。
模具表面的保護(hù)涂層損壞或失效,無法有效阻止氧氣與石墨接觸。
解決方法:
提高真空爐的真空度,減少爐內(nèi)氧氣含量。定期檢查和維護(hù)真空系統(tǒng),確保其正常運(yùn)行,保證爐內(nèi)的真空環(huán)境穩(wěn)定。
對石墨模具表面進(jìn)行抗氧化處理,如涂覆抗氧化涂層。常見的涂層材料有金屬氧化物、碳化物等,這些涂層可以在模具表面形成一層保護(hù)膜,阻止氧氣與石墨接觸,從而提高模具的抗氧化性能。
3、變形問題
原因:
高溫下石墨的強(qiáng)度降低,在承受較大壓力或自重的情況下容易發(fā)生變形。例如在燒結(jié)過程中,如果模具設(shè)計不合理或支撐不足,就可能導(dǎo)致變形。
模具的結(jié)構(gòu)和尺寸設(shè)計不合理,沒有考慮到熱膨脹系數(shù)的影響。在加熱過程中,由于不同部位的熱膨脹量不同,會產(chǎn)生內(nèi)應(yīng)力,導(dǎo)致模具變形。
解決方法:
優(yōu)化模具的結(jié)構(gòu)設(shè)計,根據(jù)石墨的材料特性和使用要求,合理確定模具的形狀、尺寸和壁厚。增加必要的支撐結(jié)構(gòu),提高模具的剛性和穩(wěn)定性,以抵抗高溫下的變形。
在模具制造過程中,充分考慮熱膨脹系數(shù)的影響,預(yù)留適當(dāng)?shù)呐蛎涢g隙或采取補(bǔ)償措施。例如,在模具的連接部位采用彈性連接方式,允許一定程度的相對位移,以緩解熱膨脹帶來的應(yīng)力。
4、磨損問題
原因:
在長期使用過程中,工件與模具表面不斷摩擦,導(dǎo)致模具表面磨損。特別是對于一些硬度較高的工件,磨損會更加嚴(yán)重。
模具表面的粗糙度較高,增加了與工件的摩擦力,加速了磨損過程。
解決方法:
對模具表面進(jìn)行拋光處理,降低表面粗糙度,減少摩擦系數(shù)。定期對模具進(jìn)行修整和維護(hù),及時修復(fù)磨損的表面,保持模具的精度和光潔度。
合理選擇模具材料和熱處理工藝,提高模具的硬度和耐磨性。例如,采用高強(qiáng)度、高耐磨性的石墨材料,或者對模具進(jìn)行表面硬化處理,如滲碳、滲氮等。
5、粘模問題
原因:
工件與模具之間的粘結(jié)力較大,在脫模時容易導(dǎo)致粘模。這可能是由于模具表面不光滑、脫模劑使用不當(dāng)或工件與模具的材料相互作用等原因引起的。
燒結(jié)過程中溫度過高或時間過長,使工件與模具之間的結(jié)合力增強(qiáng),增加了粘模的可能性。
解決方法:
改善模具表面的光潔度,使其更加光滑,減少與工件的粘結(jié)力。正確使用脫模劑,根據(jù)不同的工件材料和燒結(jié)工藝選擇合適的脫模劑種類和涂抹方式,確保脫模劑能夠均勻地覆蓋在模具表面,并且不會對燒結(jié)過程產(chǎn)生不良影響。
優(yōu)化燒結(jié)工藝參數(shù),控制好燒結(jié)溫度和時間,避免過度燒結(jié)導(dǎo)致粘模。在燒結(jié)前,可以對工件和模具進(jìn)行適當(dāng)?shù)念A(yù)熱處理,使兩者的溫度更加接近,減少因溫度差異而產(chǎn)生的熱應(yīng)力和粘結(jié)力。
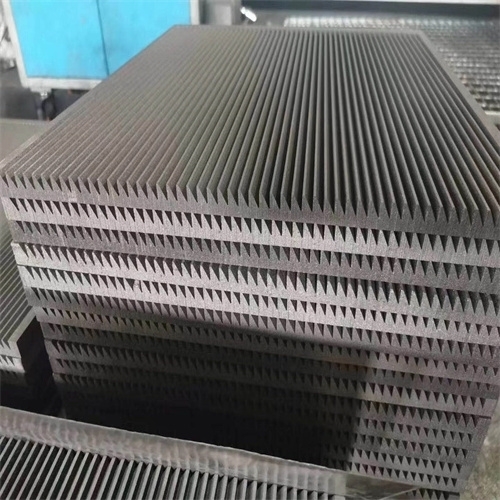